Gating systems, a vital component in casting processes, are the pathways facilitating the seamless flow of molten metal from the ladle into the mold cavity.
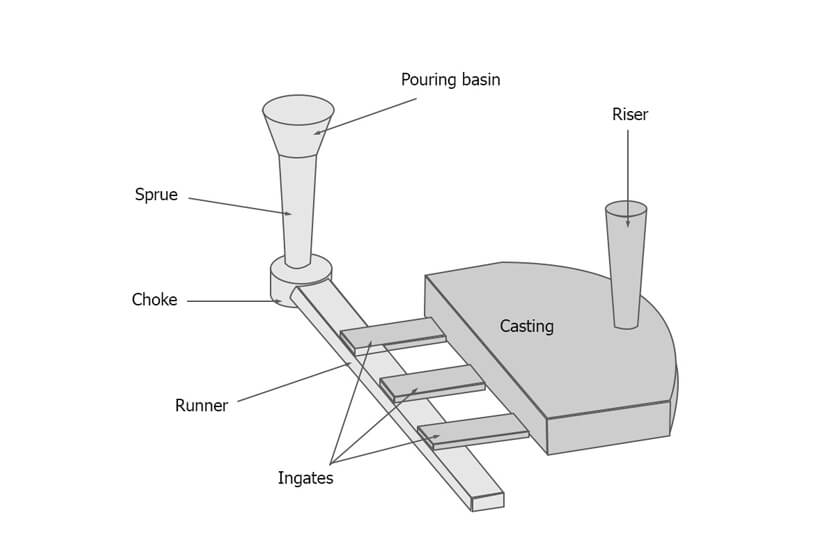
Gating system design
Understanding the design and function of these systems is fundamental to achieving flawless castings.
Let’s delve into the world of gating systems, gating items, and their role in various casting processes, along with a closer look at key terms.
Gating System Components:
A gating system comprises several crucial elements, each with a defined role:
- Pouring Basin: This initial gate entry serves as a reservoir, maintaining a steady supply of molten metal to the system.
- Sprue: Often referred to as the primary gating item, the sprue is designed with a circular cross-section to minimize heat loss and turbulence. Its dimensions are calculated based on the choke area and gating ratio, tapering from a smaller size at the bottom to a larger size at the top.
- Strut Well: This component plays a pivotal role in guiding molten metal in a controlled arc toward the runner, minimizing turbulence and aspiration. The ideal strut well shape is cylindrical, with dimensions approximately twice that of the sprue exit.
- Runner: A critical part of the gating system, the runner controls the rate of molten metal flow from the sprue to the ingate. Runner cross-sections must be larger than sprue exits and capable of filling the molten metal before it proceeds to the ingates.
- Ingate: The ingate directs the molten metal into the mold cavity, and its design is instrumental in maintaining optimal metal velocity, facilitating fettling, avoiding hot spots, and ensuring proportional metal flow relative to the cast volume.
Types of Gating Systems Based on Position:
- Horizontal System: Ideally suited for flat casting, this system relies on gravity for filling the mold cavity. It finds application in both ferrous metal sand casting and non-ferrous metal die casting processes.
- Vertical System: Tailored for tall casting applications, this system is employed in high-pressure sand casting, shell mold casting, and die casting.
- Top-Gate System: Deployed when molten metal is poured into the top space of a casting, promoting directional solidification. Its primary suitability lies in flat casting to mitigate potential metal damage.
- Bottom Gating System: Designed for tall castings, it facilitates a slow entry of molten metal from the bottom of the cavity.
- Middle Gating System: A versatile system combining features of both bottom and top gates, offering flexibility in casting design.
Gating System Significance and Key Terms:
- Gating materials play a critical role in maintaining the integrity of the gating system, ensuring efficient molten metal flow.
- Understanding what gating means is essential for achieving the desired casting quality and characteristics.
- The gating process meaning lies in its ability to control the flow of molten metal to create precise and defect-free castings.
- Proper design of the well casting component helps minimize turbulence and aspiration during the casting process.
- Spruing, another key term, refers to the process of creating the sprue, a critical gating item in casting systems.
- In settings requiring gated access, such as specialized industrial applications, well-designed gating systems are indispensable.
- Ensuring a properly configured gated entry is crucial for smooth and efficient casting operations.
- When contemplating gating items definition, it’s essential to consider factors such as casting volume and design requirements.
- Gated entry and exit points should be strategically located to optimize the flow of molten metal and minimize heat concentration.
- Gated systems are pivotal in maintaining controlled filling times, which significantly influence casting quality and properties.
In conclusion, gating systems and gating items hold a central role in casting processes, impacting the quality and characteristics of the final castings.
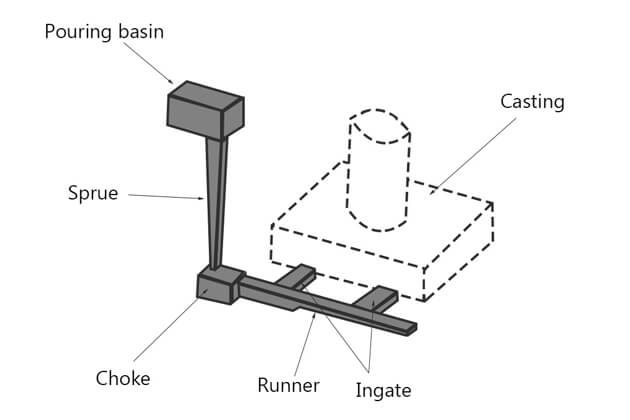
What is gating system
An understanding of these components, their design, and their significance in various casting applications is essential for achieving excellence in metal casting operations.